How to Calculate Total Cost of Ownership
When looking at the total cost of ownership, be sure to calculate energy costs, maintenance, and repair fees.
Understanding Total Cost of Ownership (TCO)
When you’re looking at new equipment, have you ever felt like the initial cost is too high?
If you answered yes, you’re not alone. The price tag can cause much confusion because it reflects one small part of the big picture. Some sources say that the amount on the price tag represents less than 10 percent of the total cost spent on a piece of equipment over its lifetime.
In fact, energy costs, maintenance, and repair fees are predicted to have at least five times more relevance than the upfront cost. But, few consider these factors as part of the price during their selection process.
To fully understand what you are paying for equipment, you need to evaluate the Total Cost of Ownership (TCO), which is an estimation of all the collective expenses associated with purchasing and operating a piece of equipment. The TCO will provide a way to compare pieces of equipment “apples to apples.”
How is Total Cost of Ownership Calculated?
try the TCO FORMULA
The next time you are selecting new equipment, try using the total cost of ownership (TCO) formula:
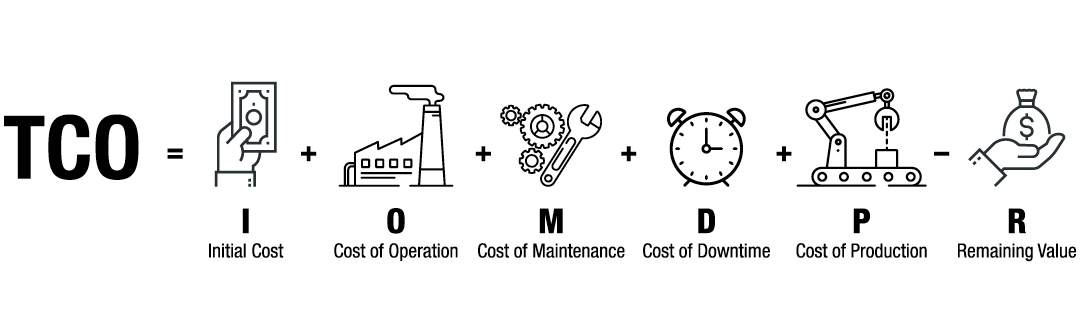
I = Initial cost
The initial cost is the number that appears on the price tag. As previously stated, this is less than 10 percent of the Total Cost of Ownership (TCO).
O = Operation
Operation is the cost to install the pump, test the pump, train employees to run the pump, and the cost of energy to operate the pump. If the pump is complicated to use, the cost of training will increase.
M = Maintenance
Maintenance includes the cost of regular repairs such as cleaning, inspecting, lubricating, and adjusting the pump to make sure it is in optimal condition. This also includes reactive maintenance when the equipment breaks down unexpectedly.
D = Downtime
While you could include downtime along with the cost of maintenance, it is often so large that it warrants its own category. Downtime involves the labor costs of employees whose work is delayed, indirect labor costs from supervisors who address the issue, lost production, and lost customers from inability to meet time expectations.
P = Production
Two different pumps will likely have different levels of output, produce different qualities, and have different environmental implications.
R = Remaining value
The remaining value has to do with the pump’s longevity. How much will the pump be worth in 5 or 10 years? It can be a big difference.
This formula can sound a little overwhelming, but let’s start simple.
I + M – R = TCO
For this example, we will start with three variables to compare two hypothetical pumps: Pump A and Pump B. The variables chosen are initial cost (I), maintenance costs over 5 years (M), and the remaining value after 5 years of depreciation (R).
- Pump A has an initial cost (I) of $10,000.
- Pump B has an initial cost (I) of $20,000, twice the upfront cost as Pump A.
Based on initial cost (I) alone, Pump A would be the clear choice. However, the TCO can tell us a lot more about which option is best.
Pump A | Pump B | |
Initial cost | $10,000 | $20,000 |
+ Maintenance | $5,000 | $2,000 |
- Remaining value | $2,000 | $10,000 |
= TCO | $13,000 | $12,000 |
The TCO of Pump B is less than Pump A even though its initial cost was twice as much. However, the gap is only $1,000, which is a slight difference.
I + M + D – R = TCO
Now add a fourth variable, estimated downtime (D).
We will go with a conservative estimate and of $50,000 per hour, even though downtime will likely be a lot more.
Pump A | Pump B | |
Initial cost | $10,000 | $20,000 |
+ Maintenance | $5,000 | $2,000 |
+ Downtime | $150,000 (3 hours at $50,000/hour) | $50,000 (1 hour) |
- Remaining value | $2,000 | $10,000 |
= TCO | $163,000 | $62,000 |
Since $163,000 – $62,000 = $101,000, pump B costs $101,000 less than Pump A. The price gap becomes wider with every variable that you add, giving you a clear choice for cost value.
Some cost savings not on the price tag
Many Graco products offer cost savings that cannot be seen on the price tag.
- E-Flo DC Circulation 4000 provides two complete motor and fluid sections that can run separately when maintenance is required. This feature minimizes the cost of downtime (D), which can easily be the highest cost for finishing companies. By calculating the estimated cost of downtime from their current equipment and comparing that to the amount of reduced downtime provided by the E-Flo DC, end-users have a much more accurate prediction of the TCO than simply by looking at the upfront cost.
- Pro Xp Electrostatic Spray Gun increases productivity (P) with a lighter and well-balanced gun body that reduces muscle strain and a built in power supply that eliminates heavy power cords that slow the operator down. It also has an ergonomic handle designed to fit comfortably in the sprayer’s hand. All of these features combine to greatly influence the cost of productivity involved in the TCO.
- ProMix PD Proportioning System reduces solvent and material waste by moving the mixing point closer to the gun. This design feature ensures that the material is mixed precisely before it is sprayed. This means that more of the expensive materials and solvents can be used for their intended purpose rather than incinerated. This especially impacts the TCO for companies who change colors multiple times per day.
Related Articles
Machine Shop Learns Not All Electrostatic Gun Brands are Equal
Graco paint spray gun provides provides the durability, quality and service needed after frustration with cheaper brand.
Trying something new? Don’t miss out on the R&D tax credit
Many manufacturers are eligible, but only 1 in 20 claim it. You may be surprised about what qualifies as research and development.
5 Ways to Reduce Unplanned Downtime
Looking for ways to stop unplanned downtime? Follow our simple tips, and downtime should not be a problem.